Welding Skill is very important for Some valve manufacture. ZECO’s pursuit of improving welding technology never stops. Last weekend, the ZECO welder have a deep communication with other skilled welder engineer after attend an welder exam local.
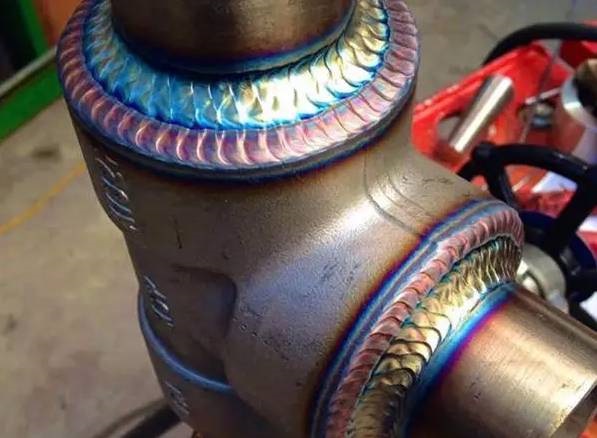
High pressure Power Plant valve fish scale weld-TIG
For the fish scale weld showed in competition,also named TIG( Tungsten invert gas welding), is a kind of welding technology. It is named for its scale-like welding plane. Its characteristic is that the pipe is directly welded to the pipe. The main thing is to select the welding point, electrify, knock out the arc with the welding rod head, melt the flux in the welding rod, and then swing the welding clamp to make the welding center melt evenly in the welding position. Should be because the general welding effect is good, it will be like fish scale, so called fish scale welding in china.
ZECO welders exchanged welding skills with each other:
1. TIG welding itself belongs to open-arc operation. It can observe the shape and flow of molten pool very well, which is much superior to electrode arc welding.
2. Controlling the hand stability during welding is the key to avoid shivering and burning the dock pole causing tungsten inclusion in the molten pool. The control method can use the index finger of the welding torch to support the welded pipe or plate. Tungsten pole extension length can be selected according to the depth of groove, generally 3 ~ 5MM.
3. The wire transport method can be selected according to the size of the groove. When the groove angle is small, the welding wire can be placed in the middle of the solution pool and continuously fed into it. When the groove is large, two side points can be used to feed the wire (to be quite skilled, avoid touching the dock pole). The welding torch moves left and right to make the edge fuse well.
4. On the surface of the full scale, according to the scoring standard of the test competition, the residual height of TIG weld is generally 0-2MM, and the surface is smooth without undercut, blowhole, crack and fusion.
While doing welding process, we come across various types of welds. Sometimes we can’t understand a specific weld type or you know very less about that. But don’t worry by reading this article you will get an exact idea about each type. In this article, you will get to know each and every type. So, what are you waiting for? Let’s have a close look….

Following are the various types of welds:
1. Fillet Weld
A fillet weld is used to join two metal pieces together at right angles or at an angle. Fillet weld is commonly known as tee joint or lap joints weld.
In T- joint, the two metal pieces are joined at the right angle to each other and in lap joints, the two metal pieces overlap each other and welded at the edges.
The weld obtained in the fillet weld is triangular in shape that may contain convex, concave, or flat surfaces depending upon the welder’s technique.
A fillet weld is used to join flanges to pipes and cross-section of infrastructure. It is also used for the welding cross-section when the bolts are not enough strong to hold it and wear off easily.
2. Groove Weld:
Groove weld is defined as an opening between the two joint members which provides the space to contain the metal. Groove welds are the most used welds after the fillet weld. There are seven basic types of groove weld:
- Square groove weld
- Single-V groove weld
- Single-bevel groove weld
- Single-U groove weld
- Single-J groove weld
- Flare-V weld
- Flare-bevel weld
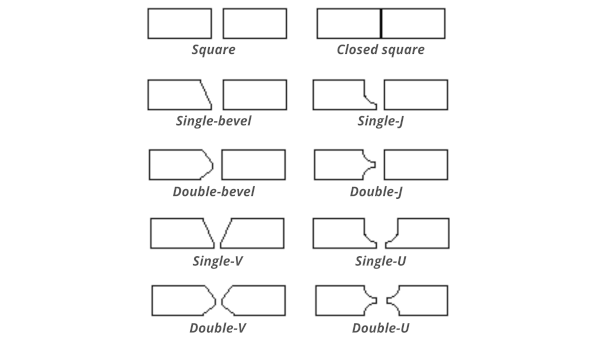
3. Surfacing Weld:
The process of deposition of a metal on another metal in order to get desired properties and dimensions with the help of a welding technique is called surfacing welding. And the weld we obtained is called surfacing weld.
4. Plug Weld
A plug weld is used to lock two metal pieces together. It is mostly used if we want to join metal with different thicknesses. These types of weld are used when we have to weld inside a pipe. The shape of the plug weld is circular.
5. Slot Weld
Basically, a slot weld join one surface of a metal to the other through an elongated cavity or hole. This cavity or hole may be partially filled with the weld metal or may be open at one end.
6. Flash Weld
Flash welding gives us a flash weld. While making the flash weld, there is no use of any type of filler metals. Here, the fusion is generated over the complete abutting (adjoining) surface. Here, heat is generated with the help of resistance to the current flow between the surfaces, and also pressure is applied to generate heat. This type of weld is used in the railroad industry.
7. Seam Weld
Seam weld is a continuous weld that is obtained between two overlapping members of a joint. Seam welding is obtained by using resistance seam welding.
8. Spot Weld
The weld that we get by doing spot welding is called spot weld. In this welding technique, the two metal pieces are joined together as spots. The adjoining surfaces of two metals have spotted at a particular distance. Look at the diagram above to understand it clearly.
In this article, we learned about the different types of welds. Hope this article gives you clear information about the different weld types. If you got some worthy knowledge out of it, share it with your friends because “Sharing is Caring”
‘Fish-scale’ is a technique of welding, known as its cataphracted weld joint. It’s regarded as the best welding technique of the world.
It’s a TIG welding method that through swing of wrist make welding nozzle rolling as the scalloped shape during welding process, it’s also known as ‘swing welding’.
How to weld a good fish scale?
1. The center of gravity
Welding is like martial arts, the first thing to do is the chassis to be stable, that is, “horse step” to be stable, not the center of gravity is not stable when shaking welding is difficult to weld a good weld.
2. The welding torch
Hand shake things can cause the formation of tungsten electrode burning molten pool the phenomenon of tungsten, weld edge is not neat, the scale size not neat, we can through the gun hand little finger and ring finger for stabilizing gun control, contact with the product can also be spread by argon arc welding of ceramic nozzle, abutting on the parts and then adjust the length of the tungsten electrode according to the depth of the crater is probably between 3 to 5 mm.
3. The wire feed stability
The method of wire feeding is adjusted according to the size of the weld groove. If the groove is small, the welding wire can be continuously fed in the center of the weld pool. When the width of the weld is large, the way of wire feeding is adopted.
“Accurate” “three accurate”
1. The parameters
Welding parameters are the key to the quality of welding, and it is very necessary to choose the correct welding parameters. Flat welding, vertical welding, according to the actual station, the actual plate thickness to choose the appropriate parameters and welding material specifications, welding current is small is not easy to arc, welding current is large is easy to weld through, molten iron next trip.
2. Accurate Angle and position
Welding gun Angle, welding position will affect the final welding molding, at the same time to avoid the emergence of welding defects (tungsten, no fusion, slag). General flat butt welding electrode swing method has zigzag, crescent, triangle, ring, and figure eight! The key of vertical fillet welding is how to control the molten pool metal. The electrode should swing up and down rhythmically according to the cooling condition of the molten pool metal.
3. time
In the welding process, when the first molten pool appears after arc initiation, the arc should be raised quickly. When the molten pool is instantly cooled into a dark red point, the arc is lowered to the arc pit, and the droplet falling overlaps with the molten pool in front by 2/3, and then the arc is raised. This rhythmically forms a fillet weld.
Method of handling rod
TIG welding is an open arc operation, which can observe the shape andflow of weld pool very clearly. The key is to keep your hand very stable and steady in welding!
Control method: Use the index finger that holding torch to support the welding plate. The length of tungsten electrode could be choose as per the depth of crevasse, usually is 3 – 5mm.
Method of handling wire
The method of handling wire should be choose as per the size of crevasse. When the size is small, welding wire could place at the middle of welding pool and continously ‘feed-in’; When the size is big, could feed the wire at two sides bit by bit, and the torch should move aroud to make sure the edge fuse well.
Welding tips
To evaluate an beautiful fish-scale welding effect, the excess weld metal of TIG welding bead should be 0 – 2mm, and the surface should be smooth. The angle, and welding current are quite important! The width and thickness should keep the same when rod moved backward, usually we make it moved upward as ‘V’ shape in vertical welding.
Plus the current is last but not least, the rod is easy to stick with plate when the current is too small; yet the plate will be punchthrough when surrent is too big. Hence current is always a hot potato to green hands or freshmen. How to deal with it when we are unskilled? JSKWED make you weld easy and easy, to press 3 seconds into our ‘simple mode’.
Which Gas Do You Need for Your TIG Weld?
No matter what you’re planning to do, your TIG weld always needs to be protected by a shielding gas. No gas and you’re going to have a very bad time. But which one works the best?
TIG gases
TIG welding will only work with inert (noble) gases. There are six inert gases, but only two of them are cheap enough to be used: argon and helium. That means picking a shielding gas is relatively simple. Pure argon is used for every application: mild steel, stainless steel and aluminium.
Helium can also be used, but it’s more expensive, so it is usually only added to argon as an extra to give more penetration. For example, if you were welding on really thick metal and you were reaching the limits of your welder’s amperage range, you could swap to an Ar/He mix. Helium is common in colder climates as well, as it burns hotter, so it provides more heat and penetration for the weld.
Why can’t semi-inert (active) gases be used?
Inert gases have only one function when being used to shield a weld: shielding the weld. They’re denser than the surrounding air, so they can completely block out any oxygen or otherwise, that would contaminate the weld. They have no effect on the welding process, and there are no changes to the arc.
On the other hand, active gases like CO2 and oxygen do have an effect on the weld. They can alter the characteristics of the arc, as well as aid with penetration, so they do more than just shield the weld.
Unlike MIG welding, which benefits from having active gases mixed in, TIG is not so forgiving. Because CO2 and oxygen affect the weld directly, it reacts badly, and the added heat can blow holes through the workpiece, plus it burns up the tungsten. By only using an inert gas like argon, the weld and your tungsten will both be properly protected.
Shielding gas protection
Shielding gases for MIG/GMAW welding
The basic gas for MIG/MAG welding is argon (Ar). Helium (He) can be added to increase penetration and fluidity of the weld pool. Argon or argon/helium mixtures can be used for welding all grades. However, small additions of oxygen (O2) or carbon dioxide (CO2) are usually needed to stabilize the arc, improve the fluidity and improve the quality of the weld deposit. For stainless steels there are also gases available containing small amounts of hydrogen (H2).
Related Tags :
Ten articles before and after
Environmental cupola is still energetic: STATE OF THE U.S. CUPOLA INDUSTRY
Mol, Thyssenkrup to establish polyol site in Hungary
Several Reasons and Preventive Measures for Flame and Explosion of Oxygen Valve, Pipeline Valve
Reasons for Rust of Stainless Steel Valves and Solution for Anti-rust
Taboos and Measures of Drainage Valve Pipeline Construction
Technical Requirements for Boiler Forging Valves-Raw Material
cryogenic application of metal sealing butterfly valve
Safety Operating Regulations for Welders-valve
Schlumberger introduces integrated seat technology ball valve
Butterfly Valve API 609 Category B