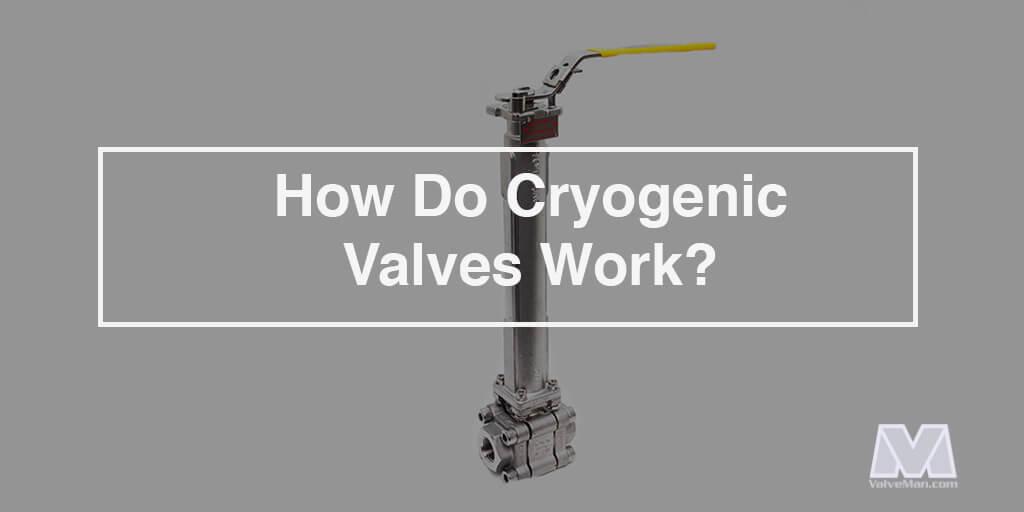
lug style butterfly valve
butterfly valve suppliers
wafer style butterfly valve
lug vs wafer butterfly valve
As its name suggests,
cryogenic valves are designed to be used in very cold applications. They are thus most popularly used by companies that work with Liquefied Natural Gas (LNG) or Compressed Natural Gas (CNG). For instance, the oil and gas industry frequently uses cryogenic temperature ranges starting at -238 degrees Fahrenheit (-150 degrees Celcius). Additionally, some gasses aren’t labeled ‘cryogenic’ because of their temperature, but rather because they require more than a simple pressure increase to compress their volume. Cryogenic valves are built to help transport and store such cryogenic gasses safely and efficiently.
Cryogenic valves differentiate from other standard valves in the modern market due to their ability to be fully functional both in temperatures as low as -320 degrees Fahrenheit (-196 degrees Celcius) and at pressure ratings as high as 750 psi.
Working Cryogenic Valves
Cryogenic valves are kept in a natural closed position to keep cryogenic gasses or other medium secure and safely contained. A cryogenic valve is generally designed to react to high pressure which pushes the valve into the open position to allow the gas or other media to flow readily through. Such open flow will continue until the pressure again decreases, at which point it will swing back nd become seal with a special metal seat bubble-tight shutoff to prevent any leaking.
Why Other Valves Can’t Cut It
Cryogenic gases and other media are extremely sensitive. Having it leak in an unwanted place can cause serious and very expensive damages, especially as it is a costly endeavor to transform standard temp gasses into cryogen.
Standard valves are sensitive to the extreme temperatures as they contract and expand at various rates when exposed to hot and freezing conditions, thus causing breaks in the seal and enabling the undesired leakage. It’s these heat gains that have long been a problem in the study, transport, and storage of cryogenic gas processing.

Choosing the Right Cryogenic Valves
There are five types of cryogenic valves that are ideal for cryogenic media. Each of these types has its own set of characteristics that make them suitable in some applications and unsuitable in others.
- Globe Valves. Called such due to their spherical shape, these valves have an internal movable disc — the obturator — that rotates at 90 degrees to the plane of its coordinated body seat. These cryogenic valves offer greater reliability for long-term sealing performance but are susceptible to moisture and aren’t good in situations where flow rate is paramount.
- Ball Valves. These valves utilize a ball as the obturator and generally include a Polytetrafluoroethylene body seat. They have better flow characteristics than globe valves but are more prone to wear and tear along its seals and the ball itself. They are thus most valuable for applications in which an unrestricted flow path is necessary.
- Top Entry Ball Valves. Similar to standard ball cryogenic valves, this newer model has a one-piece design with butt welded connections that makes maintenance easy. The lack of mechanical joints also makes it a preferred option in fire safe applications.
- Gate Valves. Gate valves utilize a wedge-type gate as the obturator which swings to close parallel to the mating body seat. They’re similar to ball valves in that they offer good flow characteristics but are hampered by wear and tear.
- Butterfly Valves. Butterfly valves are a part of the quarter turn family and utilize a circular disk at their center. This disc allows butterfly cryogenic valves to be shorter in length than the aforementioned choices, making them lighter and cheaper as well as quick and simple to operate. But over-use leads to their shorter lifspan.