4 butterfly valve dimensions
5 butterfly valve
6 butterfly valve dimensions
6 in butterfly valve
Table of Contents
- What is a Monoflange valve?
- How does a double block bleed valve work?
- Features and advantages
- What’s the difference between Monoflange valves and Keyblok valves?
- What is a pressure seal valve?
- Standard Construction features
- Pressure Seal Gate Valve
- FLEXIBLE WEDGE SEALING DESIGN
- PARALLEL SLIDE DESIGN
- Pressure Seal Globe Valve
- STRAIGHT AND Y-PATTERN SEATING DESIGN
- Pressure Seal Check Valve
- SWING CHECK AND TILT DISC
- Pressure seal design
- Pressure Seal Gate Valve
- Bolted Bonnets vs. Pressure Seals
- Standard Construction features
What is a Monoflange valve?
Monoflange valves are used to control the flow of fluids, and gases in a piping system and are available in various materials, shapes, and sizes. Monoflange Valve is a type of valve that contains one, two, or three needle valves that are fitted in a compact shaped flange body. Monoflange Needle Valves provide a reduction in dimension, volume, and weight. Slimline Monoflange Valves also reduce potential leakage points. Monoflange Valve Manufacturers recommend these flanges due to their improved performance and safety standards. Moreover, they also reduce the stress from load and vibration.
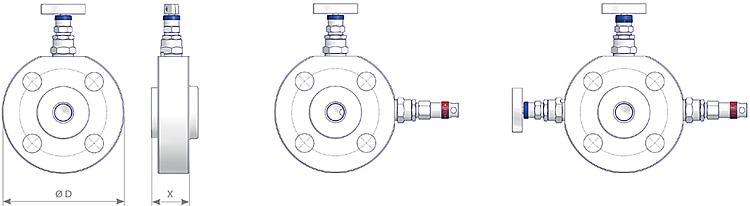
How does a double block bleed valve work?
The monoflange bodies are drilled internally with holes which connect the annular valve chambers.
The following picture illustrates the process within a DBB monoflange:
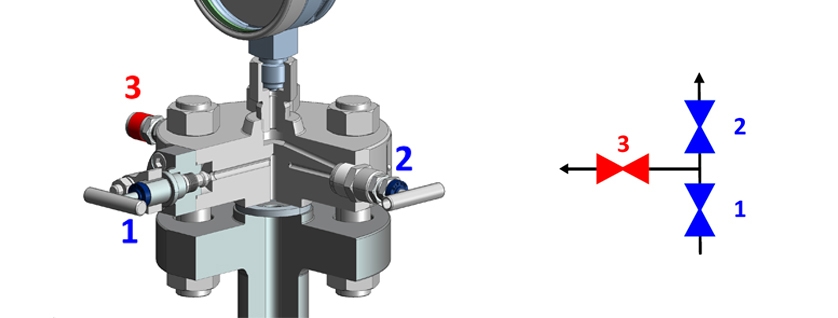
The flow enters the monoflange from the pipeline and stops below the first shut-off valve [1];
When the first shut-off valve [1] opens, the flow proceeds towards the second shut-off valve [2] ; when the valve [2] is open, the instrument is thus connected to the process line;
When the first shut-off valve [1] is closed, the medium trapped between valve and instrument can be discharged via the vent valve [3] through the vent outlet. The two shut-off valves [1, 2] are in an angled position, which allows the flow to pass through them.
The two shut-off valves allow a better isolation from the process: In case the first shut-off valve does not isolate the medium properly, the second one will act as a safety means against accidental leaks. In some cases, customer specifications do not allow the medium to be in touch with the instrument when it is not measuring. For this reason the medium shall be discharged using the vent line. In other cases – due to the vent line – instruments can be easily calibrated without dismounting them from the line.
Features and advantages
- Big variety of standard optional materials and outlet choices, mean you can pick the style you need right from the catalog
- One piece body means compact design with very low leak points
- This monoflange valves utilizes Non-rotating stem tip technology. When the stem tip get in touch with the seal, it prevents rotating, stopping the cross scoring and final leaks that can happen with all ball stems.
- 4 rings PTEE Chevron style packing, or multi-ring set of gasoil bordered by graphite standard. These standard packing sets are 3rd party verified to exceed US EPA 40 CFR sixty emission standards by more than five times. Less probability of leaks mean less danger.
- Top standard metal to metal shutoff ANSI class. VI criteria force equipment directive.
What’s the difference between Monoflange valves and Keyblok valves?
Monoflange valves and Keyblok valves are both types of primary isolation valves used to isolate the process media from a given location, often for safety or maintenance purposes. They are typically installed within an instrument hook up loop as the “take off valve” or the “first valve” off from the process flow line. This safely isolates instrumentation devices from the process media while still meeting piping class codes and standard valve requirements. Monoflange and Keyblok valves can be arranged for use in many applications including instrument isolation, gauge/pressure isolation, instrument drain, and chemical injection/ sampling.
While both types of valves serve a similar purpose, they do have some distinct differences and applications listed below:
Monoflange type | Keyblok Type | |
Bore Size | 3/8″~2″ | |
Valve & Bonnet Type | Globe Style Pattern *Rising Ball End Stem *Screwed or Bolted Bonnet *Integral Sea | Floating Type Ball Valve *Metal or Soft Seat Optional Globe Style Pattern *Venting *Rising Ball End Stem *Screwed Bonnet *Integral Seat |
Inlet Connection Types | *Flanged | *Flanged *Screwed *Welded |
Outlet Connection Types | *Threaded *Welded | *Threaded *Flanged |
Body Type | Forged body compact wafer style | Forged body with one, two or three piece design |
Valve Configurations | *Block *Block & Bleed *Double Block *Double Block & Bleed | |
Installation | *Compact Envelope *Lower Weight *Best for use on lighter hydrocarbons or non-plugging fluids | *Roddable multiple size bore(s) *Compact Envelope versus typical assembly of standard multiple isolation valves *Best for use on heavier hydrocarbons or plugging fluids *Available for langed outlets |
Quality | Meets line class piping codes and standards,fire safe and bubble tight for instrument shut off | |
Cost | *Both have a lower installation cost compared to individual valve assemblies *Single body design results in negligible non-destructive examination (NDE) requirements/Cost-ex: PMI, MPE, DPE *Monoflanges are typically less expensive than keybloks due to orifice size |
What is a pressure seal valve?
Pressure seal construction is adopted for Valves for high pressure service, typically in excess of above 170 bar. The unique feature about the pressure seal Bonnet is that the body-Bonnet joints seals improves as the internal pressure in the Valve increases, compared to other constructions where the increase in internal pressure tends to create leaks in the body-Bonnet joint.
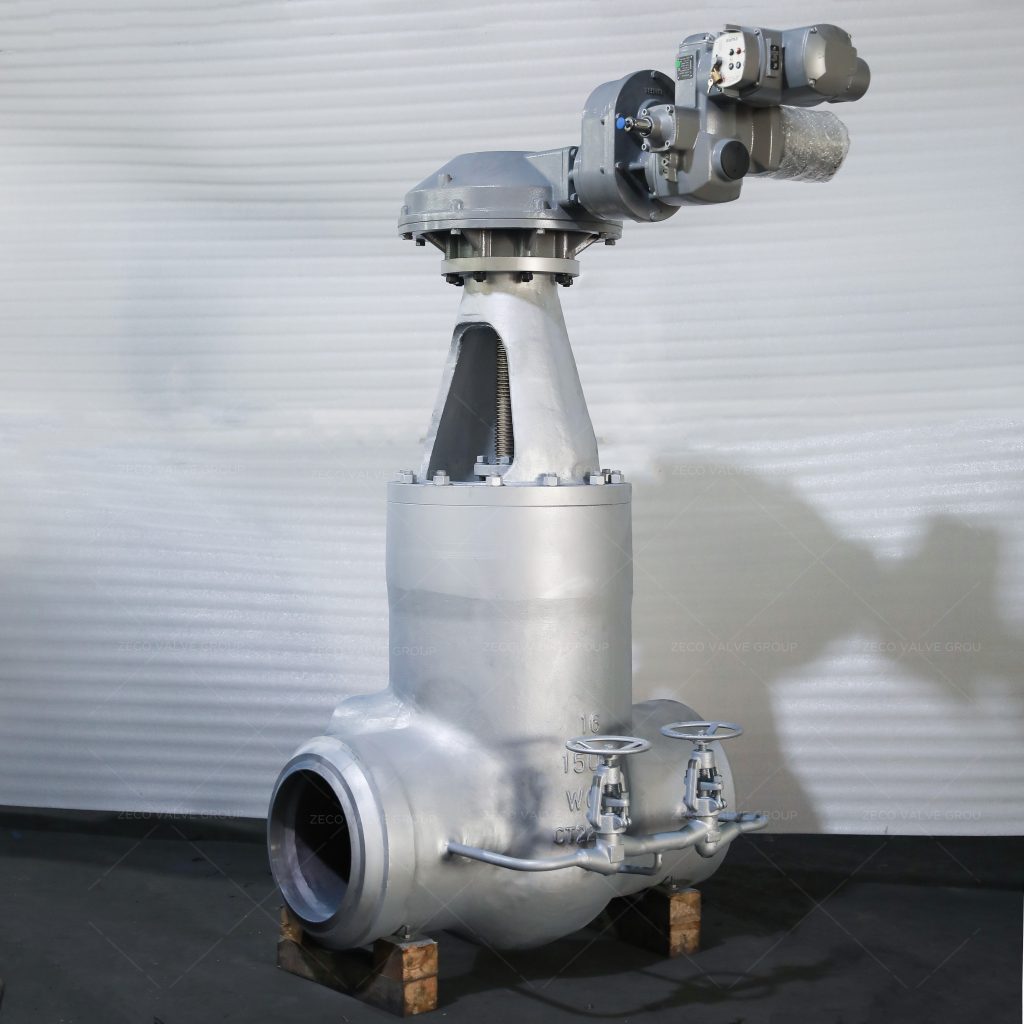
Standard Construction features
Pressure Seal Gate Valve
FLEXIBLE WEDGE SEALING DESIGN
The flexible wedge is a one-piece, fully guided cast wedge with a central hub to allow the seating faces to move relative to each other, thus compensating for distortion of the body seats due to thermal expansion or piping loads. Seat ring and wedge seating face are set at a 9° angle from vertical to minimize sliding contact of the wedge and seat ring during opening and closing.
Wedging actions help effect a tight seal in low differential pressure services. Flexible wedge construction resists wedge sticking or binding in services where the valve may be closed when cold and opened when hot. Seating surfaces are hardfaced with Stellite®6 to provide high life cycle capability in very high differential pressure services
PARALLEL SLIDE DESIGN
The gate is a split design using two discs spring loaded and held together by a gate holder with a corrosion reservior spring to provide initial energizing when closed. The gate relies for seat tightness on the primary fluid pressure acting on the downstream seat. There is no wedging action or extra loading on the seats resulting in considerably lower operating torque. During closing there is a bevel on the bottom of the gate to guide it in between the seats and recompress the spring. Seating surfaces are hardfaced with Stellite®6 to provide high cycle capability in very high differential pressure services.
Pressure Seal Globe Valve
STRAIGHT AND Y-PATTERN SEATING DESIGN
All DSI globe valves utilize a seating design that consist of a guided disc which seals fully with the seat to provide a tight seal. Seating surfaces are hardfaced with Stellite®6 to increase the life cycle.
All DSI globe valves are unidirectional.
Pressure Seal Check Valve
SWING CHECK AND TILT DISC
Pressure Seal check valves are designed for reliability in high velocity service applications to prevent backflow. The check valves are designed to operate in either vertical upflow or horizontal pipe runs. Seating surfaces are hardfaced with Stellite®6 to provide high life cycle capability.
The swing check design offers a higher flow coefficient than a tilting disc design with higher flow area. The tilting disc is a non-slam design.
Pressure seal design
A/B – Bonnet tendency to move up or down as pressure changes
C – System pressure
D – Sealing forces due to pressure
The higher the internal pressure, the greater the sealing force. Easy dismantling is made possible by dropping the Bonnet assembly into the body cavity and driving out the four-segmental thrust rings by means of a push pin.
Bolted Bonnets vs. Pressure Seals
To better understand the pressure seal design concept, let’s contrast the body-to-Bonnet sealing mechanism between bolted Bonnets and pressure seals. Fig. 1 depicts the typical Bolted Bonnet valve. The body flange and Bonnet flange are joined by studs and nuts, with a gasket of suitable design/material inserted between the flange faces to facilitate sealing. Studs/nuts/bolts are tightened to prescribed torques in a pattern defined by the manufacturer to affect optimal sealing. However, as system pressure increases, the potential for leakage through the body/Bonnet joint also increases.
Now let’s look at the pressure seal joint detailed in Fig. 2 Note the differences in the respective body/Bonnet joint configurations. Most pressure seal designs incorporate “Bonnet take-up bolts” to pull the Bonnet up and seal against the pressure seal gasket. This in turn creates a seal between the gasket and the inner dia (I.D.) of the valve body.
A segmented thrust ring maintains the load. The beauty of the pressure seal design is that as system pressure builds, so does the load on the Bonnet and, correspondingly, the pressure seal gasket. Therefore, in pressure seal Valves, as system pressure increases, the potential for leakage through the body/Bonnet joint decreases.
This design approach has distinct advantages over bolted Bonnet Valves in main steam, feedwater, turbine bypass, and other power plant systems requiring Valves that can handle the challenges inherent in high-pressure and temperature applications.
But over the years, as operating pressures/temperatures increased, and with the advent of peaking plants, this same transient system pressure that aided in sealing also played havoc with pressure seal joint integrity.
Related Tags :
ZECO Valve
Gate Valve vs Ball Valve
NBR Butterfly Valve
What is an Axial Check Valve
Gate Valve Repair
What is a Globe Valve?
Manual Operate Gate Valve Manufacturer
What are Globe Valves?
Difference Between Gate Valve And Butterfly Valve
Ten articles before and after
New Energy power plant gate valve,molten salt control valve,solar thermal power plant control valve – Titanium ball valves supplier china,Cryogenic Globe Valve manufacturers china,C95800 butterfly valve in china,Bellow sealed globe valve factory,inconel 625 globe valve company | Professional valve manufacturer
Intelligent electrical actuator control valve,wastewater treatment gate valve – Titanium ball valves supplier china,Cryogenic Globe Valve manufacturers china,C95800 butterfly valve in china,Bellow sealed globe valve factory,inconel 625 globe valve company | Professional valve manufacturer
Marine check valve,Seawater check valve,C95800 ball valve – Titanium ball valves supplier china,Cryogenic Globe Valve manufacturers china,C95800 butterfly valve in china,Bellow sealed globe valve factory,inconel 625 globe valve company | Professional valve manufacturer
automatic ball valves,mono flange needle valve – Titanium ball valves supplier china,Cryogenic Globe Valve manufacturers china,C95800 butterfly valve in china,Bellow sealed globe valve factory,inconel 625 globe valve company | Professional valve manufacturer
automatic ball valve,automatic butterfly valve – Titanium ball valves supplier china,Cryogenic Globe Valve manufacturers china,C95800 butterfly valve in china,Bellow sealed globe valve factory,inconel 625 globe valve company | Professional valve manufacturer
High performance butterfly valve ,metal to metal seat butterfly valve,64” RF butterfly valve – Titanium ball valves supplier china,Cryogenic Globe Valve manufacturers china,C95800 butterfly valve in china,Bellow sealed globe valve factory,inconel 625 globe valve company | Professional valve manufacturer
Ball valve for sea water, C95800 ball valve – Titanium ball valves supplier china,Cryogenic Globe Valve manufacturers china,C95800 butterfly valve in china,Bellow sealed globe valve factory,inconel 625 globe valve company | Professional valve manufacturer
Natural Gas plants ball valves,power plant high pressure high temperature gate valves – Titanium ball valves supplier china,Cryogenic Globe Valve manufacturers china,C95800 butterfly valve in china,Bellow sealed globe valve factory,inconel 625 globe valve company | Professional valve manufacturer
renewable energy control valves,molten salt control valves – Titanium ball valves supplier china,Cryogenic Globe Valve manufacturers china,C95800 butterfly valve in china,Bellow sealed globe valve factory,inconel 625 globe valve company | Professional valve manufacturer
high pressure high temperature steam gate valves,power plant Rotork actuator globe valves – Titanium ball valves supplier china,Cryogenic Globe Valve manufacturers china,C95800 butterfly valve in china,Bellow sealed globe valve factory,inconel 625 globe valve company | Professional valve manufacturer